BOMs, Assemblies, and more working in sync
Improving Manufacturing experiences with integrations
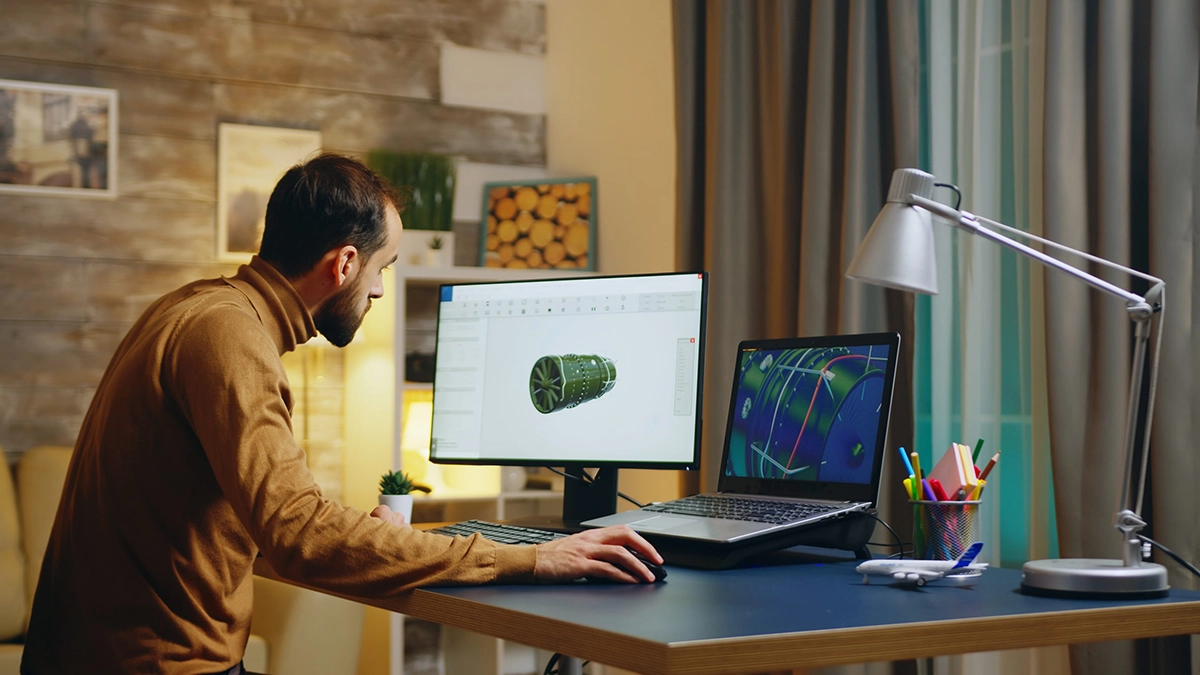
How Initus integrations benefit the Manufacturing industry
How Initus integrations benefit the Manufacturing industry
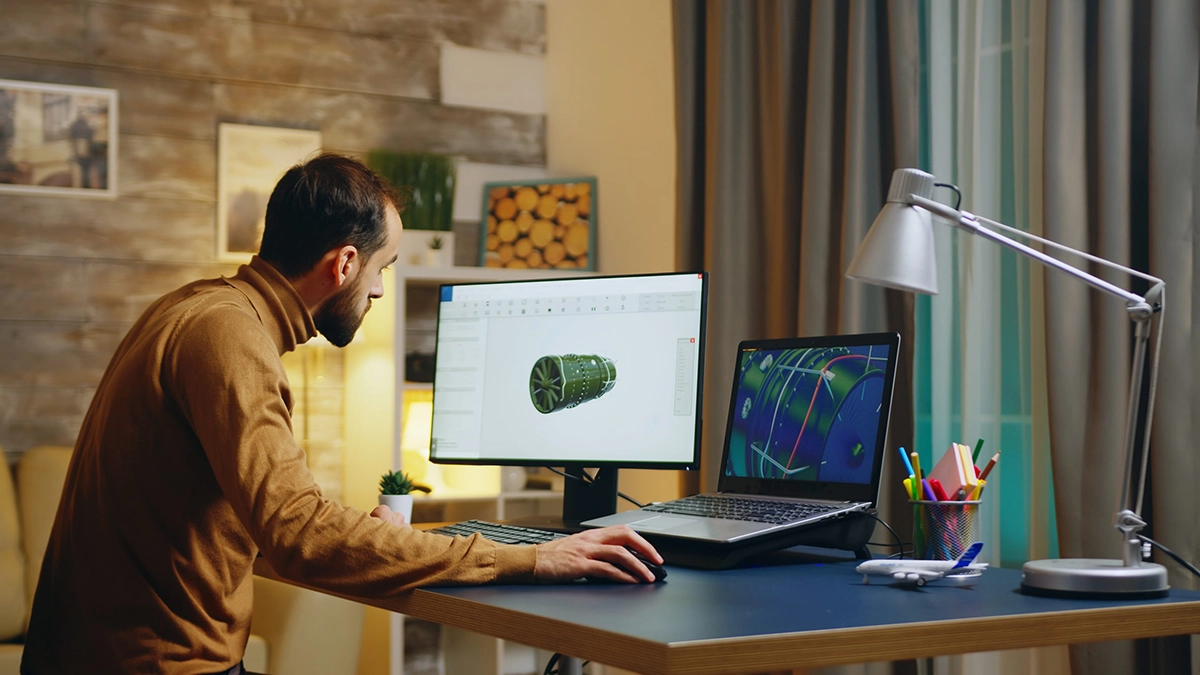
Initus can resolve manufacturing industry challenges via integrations
The challenges
The solutions
01 – Disconnected Manufacturing Systems
Manufacturing companies often face the challenge of disconnected systems across various departments, such as production, inventory, quality, and supply chain management. Consequently, this can lead to data silos, which in turn hinder communication, thereby creating inefficient processes and a lack of visibility into the end-to-end manufacturing operations.
02 – Manual Data Entry and Paper-Based Processes
Due to the lack of integrated systems, manufacturing teams may rely heavily on manual data entry and paper-based processes. This reliance can lead to errors, delays, and inefficiencies in capturing and processing crucial data, including production orders, material requisitions, or quality inspections.
03 – Lack of Real-Time Production Visibility
As a result of disconnected manufacturing systems, there is often a lack of real-time visibility into production activities, inventory levels, and supply chain status. This lack of visibility can significantly challenge manufacturing teams in monitoring production progress, managing inventory levels effectively, and making timely and informed decisions.
04 – Inefficient Production Planning and Scheduling
Furthermore, the lack of integration between production planning, scheduling, and execution systems can contribute to inefficiencies within the manufacturing process. Specifically, this can result in suboptimal production plans, increased lead times, machine idle times, and difficulties in adapting to dynamic customer demands or changing production requirements.
05 – Compliance and Traceability Issues
Finally, disconnected systems can pose significant challenges in ensuring compliance with quality standards, traceability requirements, and regulatory obligations. For instance, the lack of integrated quality management systems, proper documentation control, or effective traceability tools can hinder manufacturers’ ability to track and trace products, meet regulatory requirements, and maintain consistent quality standards.
01 – Integrated Manufacturing Systems
By integrating manufacturing systems such as Enterprise Resource Planning (ERP), Manufacturing Execution System (MES), and Warehouse Management System (WMS), a seamless flow of information is achieved across different departments. This integration improves communication, eliminates data silos, and consequently allows for better coordination of manufacturing operations.
02 – Automation of Data Capture and Workflows
Furthermore, integrations can automate data capture from machinery, equipment, and other production systems. As a result, manual data entry is eliminated, reducing errors and enabling real-time data collection for more informed decision-making. Moreover, automated workflows can streamline processes, such as production order creation, material requisition, or quality inspections.
03 – Real-Time Production Monitoring and Analytics
Importantly, integration enables real-time visibility into production activities, inventory levels, and supply chain status. This real-time visibility allows manufacturing teams to monitor production progress, identify bottlenecks, manage inventory levels more efficiently, and ultimately make data-driven decisions to optimize production processes.
04 – Integrated Production Planning and Scheduling
In addition, integrating production planning, scheduling, and execution systems improves the accuracy and efficiency of production planning. This integration enables manufacturers to create optimal production plans, schedule resources effectively, adapt to changing demands, and therefore reduce lead times and machine idle times.
05 – Quality Management and Traceability Enhancements
Finally, integrating quality management systems and traceability tools helps manufacturers ensure compliance with quality standards and regulatory obligations. This integration enables efficient tracking and tracing of products, facilitates product recalls if necessary, and provides necessary documentation for compliance audits.
The challenge
01 – Disconnected Manufacturing Systems
Manufacturing companies often face the challenge of disconnected systems across various departments, such as production, inventory, quality, and supply chain management. Consequently, this can lead to data silos, which in turn hinder communication, thereby creating inefficient processes and a lack of visibility into the end-to-end manufacturing operations.
02 – Manual Data Entry and Paper-Based Processes
Due to the lack of integrated systems, manufacturing teams may rely heavily on manual data entry and paper-based processes. This reliance can lead to errors, delays, and inefficiencies in capturing and processing crucial data, including production orders, material requisitions, or quality inspections.
03 – Lack of Real-Time Production Visibility
As a result of disconnected manufacturing systems, there is often a lack of real-time visibility into production activities, inventory levels, and supply chain status. This lack of visibility can significantly challenge manufacturing teams in monitoring production progress, managing inventory levels effectively, and making timely and informed decisions.
04 – Inefficient Production Planning and Scheduling
Furthermore, the lack of integration between production planning, scheduling, and execution systems can contribute to inefficiencies within the manufacturing process. Specifically, this can result in suboptimal production plans, increased lead times, machine idle times, and difficulties in adapting to dynamic customer demands or changing production requirements.
05 – Compliance and Traceability Issues
Finally, disconnected systems can pose significant challenges in ensuring compliance with quality standards, traceability requirements, and regulatory obligations. For instance, the lack of integrated quality management systems, proper documentation control, or effective traceability tools can hinder manufacturers’ ability to track and trace products, meet regulatory requirements, and maintain consistent quality standards.
The solutions
01 – Integrated Manufacturing Systems
By integrating manufacturing systems such as Enterprise Resource Planning (ERP), Manufacturing Execution System (MES), and Warehouse Management System (WMS), a seamless flow of information is achieved across different departments. This integration improves communication, eliminates data silos, and consequently allows for better coordination of manufacturing operations.
02 – Automation of Data Capture and Workflows
Furthermore, integrations can automate data capture from machinery, equipment, and other production systems. As a result, manual data entry is eliminated, reducing errors and enabling real-time data collection for more informed decision-making. Moreover, automated workflows can streamline processes, such as production order creation, material requisition, or quality inspections.
03 – Real-Time Production Monitoring and Analytics
Importantly, integration enables real-time visibility into production activities, inventory levels, and supply chain status. This real-time visibility allows manufacturing teams to monitor production progress, identify bottlenecks, manage inventory levels more efficiently, and ultimately make data-driven decisions to optimize production processes.
04 – Integrated Production Planning and Scheduling
In addition, integrating production planning, scheduling, and execution systems improves the accuracy and efficiency of production planning. This integration enables manufacturers to create optimal production plans, schedule resources effectively, adapt to changing demands, and therefore reduce lead times and machine idle times.
05 – Quality Management and Traceability Enhancements
Finally, integrating quality management systems and traceability tools helps manufacturers ensure compliance with quality standards and regulatory obligations. This integration enables efficient tracking and tracing of products, facilitates product recalls if necessary, and provides necessary documentation for compliance audits.
Start shaping the future of your business
Today is a great day to optimize your
Sales Operations Audit Process e-Commerce Channel Data Migration Project Procurement Process Inventory Management
with Initus
Our Custom Solutions
Unlock the full potential of your manufacturing facility
Designed for Simplicity, Built for Power
Whether you need standard integrations or want to tap into the power of AI, InitusIO offers a complete solution. What sets us apart? Our seamless setup, expert support, and ability to handle both regular and AI-enhanced integrations with ease.
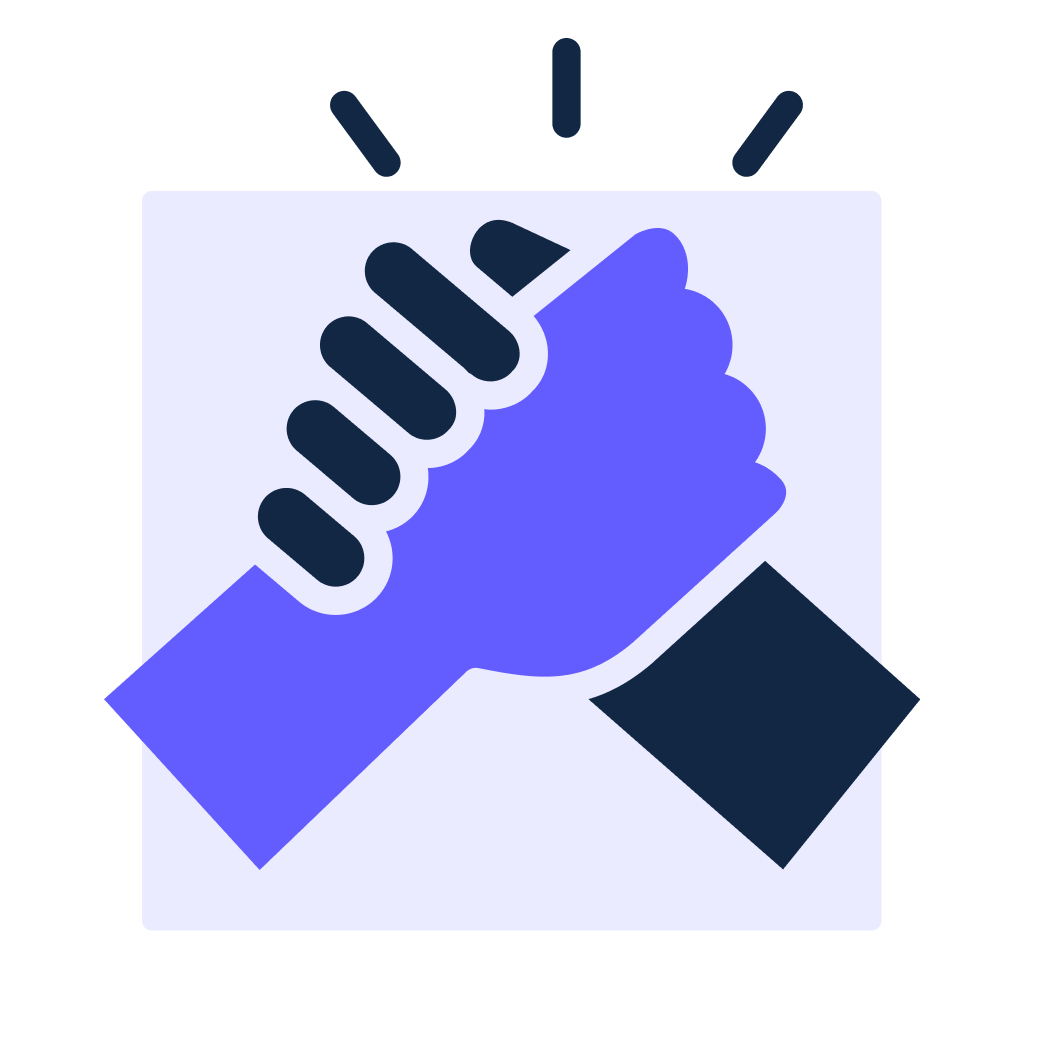
Tailored for Your Business
We assess your unique needs and design integrations to drive efficiency in the processes that matter most.
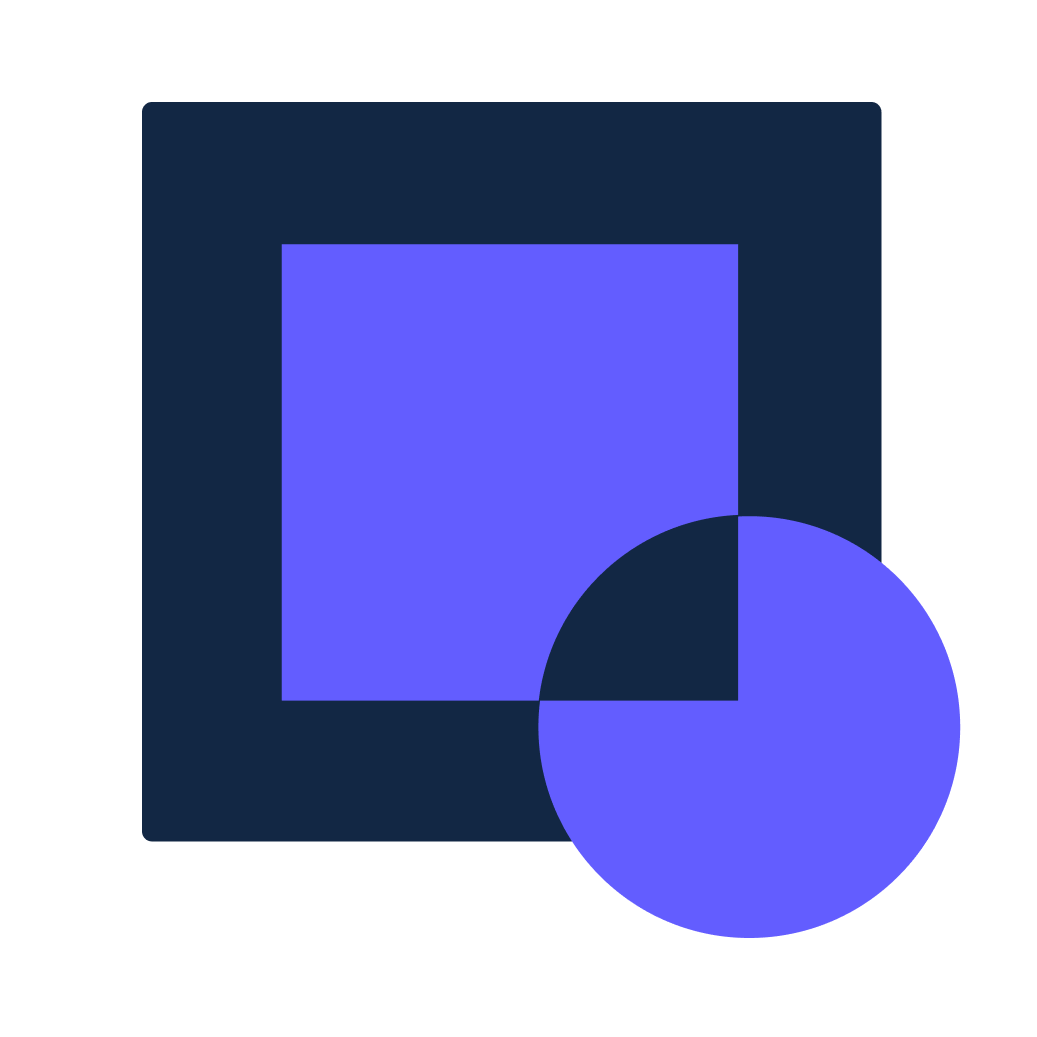
Quick and Seamless Integration
Skip the complexities—our turnkey solution is built for fast, seamless deployment.
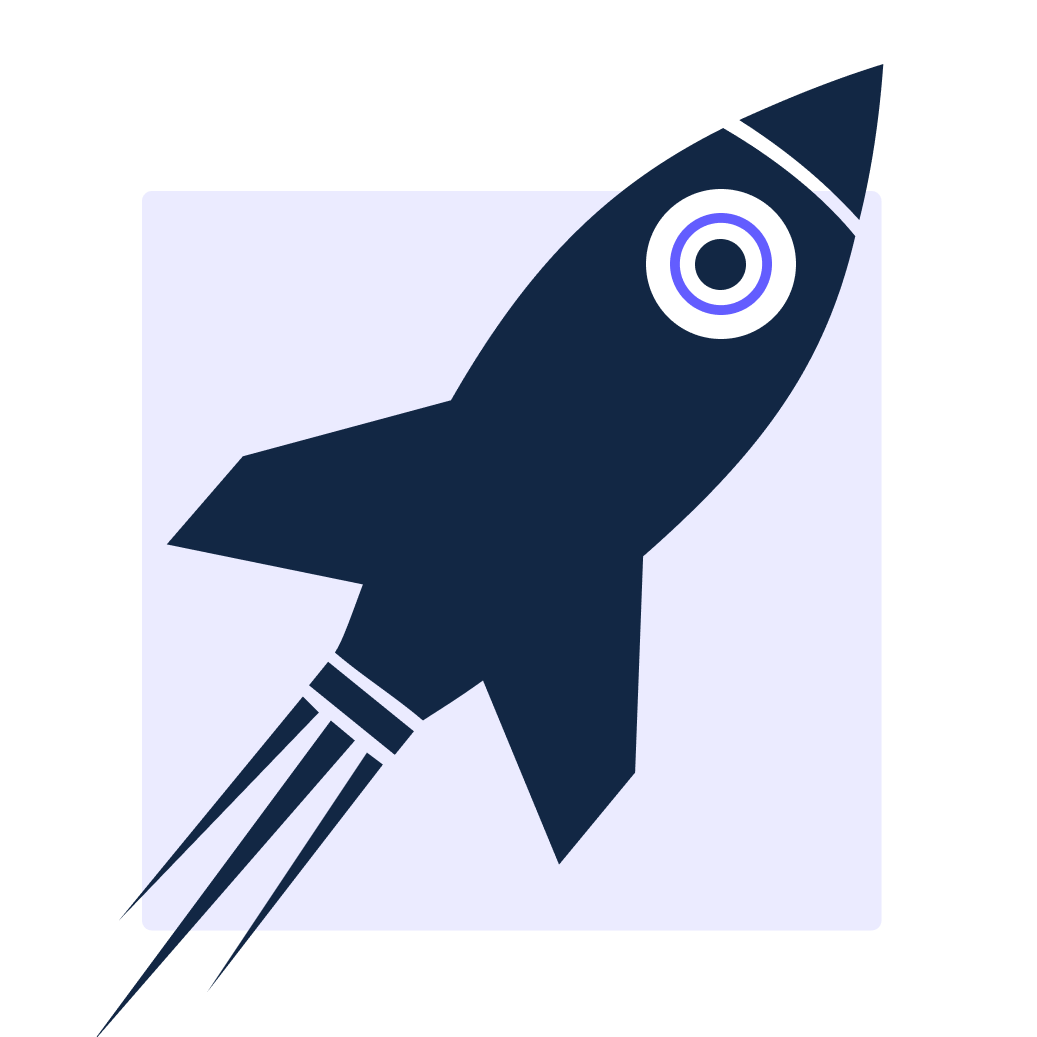
Scalable and Secure
InitusIO grows with your business, ensuring scalability and security at every step.